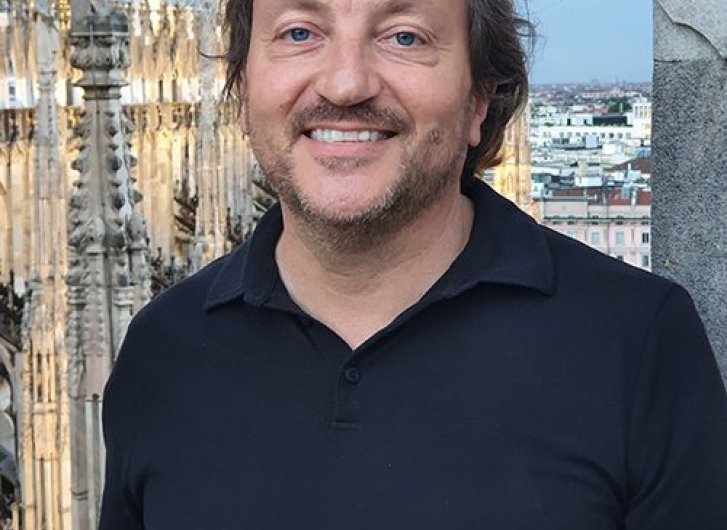
Mirage and sustainable manufacturing.
What was your first step towards sustainability?
Care of the environment has always been a factor in our policy and the first investments in energy and resource-saving go back a few years now: in 2012, we invested in our first completely electric machine (an injection press, to be precise) which eliminated the use of oil thanks to its power inverter engines. I can safely say that what distinguishes us from other companies is our sustainable manufacturing.
Can you explain this concept to us in more detail?
One of the various measures we implemented for more eco-friendly production included the investment in sifters. Grilamid and nylon are very hard materials and need various sifters which are different from those used in acetate manufacturing, otherwise the production times are too long; so, our sifting plants are water-based. As the process requires 100 litres of water every 45-60 minutes, our daily water consumption could easily go over 3,000 litres a day. To combat this waste, we set up a modern filtering system (a purifier) with water salvaging, which allows us to replace the water just once every six months.
Then, for a few years now, we have used a 100% LED lighting system and our solar panels system allows us to produce 50% of our energy requirements while the other half is provided by our energy supplier who uses completely renewable sources.
33% of the pressing system is completely electric, guaranteeing an annual saving of 200 kg of oil per machine, and thus a significant energy saving. The same press machines are cooled by a closed water system, using chillers that recycle air to lower the temperature.
So, a policy that expands in various directions…
Absolutely! We have also begun working to achieve UNI EN ISO 14001-15 certification, aimed at establishing and implementing a system of environmental management. The goal is to achieve certification by February 2022.
How is this virtuous approach passed on to your employees?
With a training course aimed at changing their attitudes regarding environmental issues, translated into precise steps to improve both production and product.
Two innovations have been offered by your company in recent months: the launch of the 23 Eyewear brand, and the partnership agreement for production and distribution of North Sails sunglasses. Can you tell us how these two projects are sustainable?
23 Eyewear has been set up in partnership with Studio Russo of Milan. The collection uses Neocleus, a regenerated material derived from manufacturing waste material in the moulding process and from frames. The same material is treated to allow endless recycling. The frames are equipped with a hinge that is tightened but designed to be later disassembled and recycled at the product’s end of life. To round off, the glasses’ lenses are in glass, a material that can be melted down and used again for other purposes.
The North Sails glasses, our first licenced range, stand out for their use of technical materials (also floating), which are eco-friendly and recycled (such as in fishing rods). The collection, like all our glasses, is produced according to our “Zero Waste” philosophy, to minimise waste materials during production.
For the packaging, too, we chose to use only recycled or biodegradable materials.
What is your next step towards sustainability?
Our next step involves completing a product LCA to establish the environmental effect of our production; the results will help us improve each year in terms of product and process, to support the environment and public health.